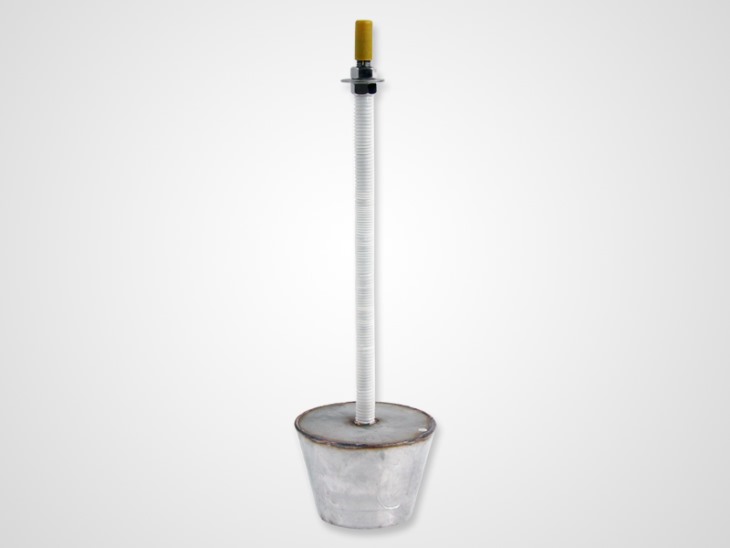
The inside of the gas diffuser is made of high-purity corundum material with high temperature resistance, and the outer shell is made of heat-resistant stainless steel. Because the outer shell material is "non-magnetic" and resistant to a certain temperature, it is suitable for the bottom of the induction furnace; the internal refractory material is a diffused pore structure , The gas channel is composed of tiny and through pores. The particle size design of the refractory material makes the gasification and resistance to the penetration of the molten metal. When using a certain pressure and flow of gas (argon, nitrogen, etc.), it can be generated in the molten metal. A large number of tiny and evenly dispersed bubbles will have a refining effect on the molten metal as the bubble flow composed of countless tiny bubbles rises.
Gas diffusers can be used in a wide range of metal and alloy smelting, such as stainless steel, alloy steel, aluminum alloy, copper alloy, etc.; can be used in induction furnaces, can also be used in ladle;
For the special gas diffuser for the aluminum industry, specific additives need to be added when the refractory material is batched. After the material is fired, a thin layer will be formed around the alumina particles. The thin layer material can change the wetting angle of the molten aluminum, thereby preventing the molten aluminum. Adhesion to the diffuser. The aluminum diffuser shell is generally made of grade 310 stainless steel. No matter whether the gas is argon, nitrogen or chlorine, the diffuser has a long service life, generally used for about 2 years. Mainly used in aluminum melting furnaces , holding furnace, degassing box, etc.
Application of Gas Diffuser - Refining Technology of Intermediate Frequency Induction Furnace
Through the use of gas diffusers, we have summed up the refining technology of intermediate frequency induction furnaces, so that ordinary intermediate frequency induction furnaces can be transformed from "chemical steel" to steelmaking. In many cases, the quality of molten steel (Taijin) reaches AOD furnaces, LF refining Furnace, VD vacuum degassing furnace refining quality level.
The required gas (such as high-purity argon) is sent to the molten steel through the gas diffuser, and after a certain amount and time of flow 8, it can reduce the inclusions (such as Sio2, Al2O3, MgO, etc.). And 【O】【 The effect of N] [H] content, there are special requirements such as decarburization, argon\/oxygen mixed gas can be blown in, which can reduce the amount of carbon in a certain range, and nitrogen can be blown in to increase ammonia when it encounters nitrogen steel.
\u003Ci>工作原理感应炉内吹入氩气精炼过程是在钢液熔清后.\u003C\/i> \u003Cb>Working principle The refining process by blowing argon into the induction furnace is after the molten steel is melted.\u003C\/b>\u003Ci>进行预脱氧完成后,取样分析后,将高纯度氩气通过安装在炉子底部的气体扩散器导入钢液,当氩气通过气体扩散器后,因分散度较高,形成了具有较大上升速度的微小气泡流,无数的气泡通过钢液将会产生精炼作用.钢液内部每个氩气泡就是一个小的"真空室",在氩气泡里不合H,O,N等气体.\u003C\/i> \u003Cb>After the pre-deoxidation is completed, after sampling and analysis, high-purity argon gas is introduced into the molten steel through the gas diffuser installed at the bottom of the furnace. The flow of tiny bubbles, countless bubbles will produce refining effect through the molten steel. Each argon bubble inside the molten steel is a small "vacuum chamber", and there is no H, O, N and other gases in the argon bubble.\u003C\/b>\u003Ci>也就是说氩气泡里面这些气体的分压力等于零.当分压力变很高的氩气泡,穿过钢液时,呈溶解状态存在的【H】【O】【N】和非溶解状态存在的c0等均会自动地进入氩气泡内,并随着气泡上升而溢出.\u003C\/i> \u003Cb>That is to say, the partial pressure of these gases in the argon bubble is equal to zero. When the partial pressure of the argon bubble becomes very high, when it passes through the molten steel, [H] [O] [N] exists in a dissolved state and c0 exists in a non-dissolved state, etc. All will automatically enter the argon bubble and overflow as the bubble rises.\u003C\/b>\u003Ci>从而达到脱气的目的.\u003C\/i> \u003Cb>So as to achieve the purpose of degassing.\u003C\/b>
\u003Ci>精炼后钢的质量,纯净度大大提高,精炼前后的夹杂物对比明显降低,气体含量大大减少.\u003C\/i> \u003Cb>The quality and purity of the steel after refining are greatly improved, the contrast of inclusions before and after refining is significantly reduced, and the gas content is greatly reduced.\u003C\/b>\u003Ci>现举例对比如下\u003C\/i>\u003Cb>The example is compared as follows\u003C\/b>
1. Inclusions: Microscopic evaluation method for non-metallic inclusions in steel GB10561-2005
project | A | B | C | D |
Sulfide | Alumina | Silicate | Globe oxide | |
Average before refining | 1.8class | 1.7class | 1.5class | 2.1class |
Average after refining | 0.55class | 0.64class | 0.5class | 0.67class |
Average percentage reduction | 69 | 62 | 67 | 68 |
The measured results fully meet the standard technical requirements.
2. The hydrogen content is less than 1.0ppm, which meets the requirements of die steel and is less than or equal to 2.5ppm, and other steel types are less than or equal to 3.0ppm.
3. The oxygen content is less than 0.0050%.
4. After the ingot is processed, the ultrasonic testing all reach the (GB\/T13315-1991) level 2 standard.
5. Comparison of mechanical properties between refined and unrefined stainless steels such as 304: (GB\/T328-2002)
1) The tensile strength before refining is 549.53Mpa, and after refining, 606.82Mpa is increased by 57.29Mpa
2) Yield strength before refining 270Mpa after refining 339.52Mpa increased by 69.52Mpa
3) 38.46KN before power refining, 49.10KN after refining, increased by 10.64KN
A few notes:
a) Since the argon blowing time for each furnace is 510mm, argon blowing is carried out after the addition of gold, and the tapping after blowing will not affect the smelting time and will not increase the power consumption.
b) The removal of [N] [H] [O] by blowing argon does not have a chemical reaction, which not only does not shorten the life of the furnace lining, but also prolongs the life of the furnace lining due to the homogenization of the melt temperature in the furnace.
c) Argon is an inert gas and is very safe to use.
In a nutshell: the medium frequency induction furnace refining technology marked by the use of gas diffusers is a production process with less investment, quick effect, low cost and high quality. It is an energy-saving and environmentally friendly production process and a short process. The production process. Based on this technology, with the protection of the casting process, high-quality castings and steel products can be produced.
The smelting experts of Quantong Kiln are willing to serve you and provide suggestions for your product quality improvement, smelting cost reduction, new product development and other issues of interest to you.
high qualityIntermediate frequency furnace refiningService Looking for Luoyang Luoyang Quantong Kiln Industry Co., Ltd.