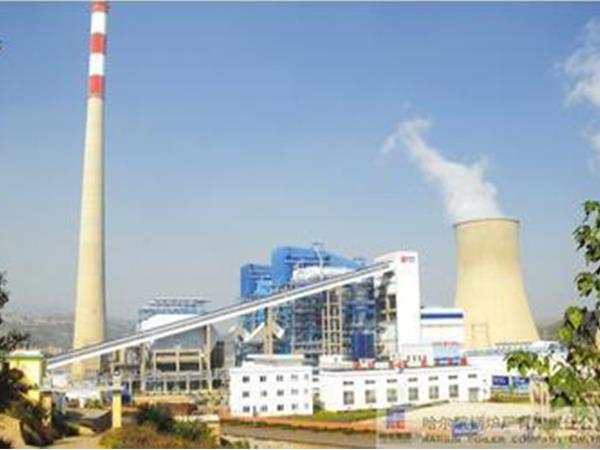
Characteristics of Circulating Fluidized Bed Boilers and Requirements for Furnace Lining Refractories
Circulating fluidized bed boiler is an oil and clean combustion technology of coal developed in the 1970s. It was introduced into my country in the 1980s. At the end of the 20th century, my country formed its own relatively mature technology. Due to the environmental protection and energy saving of circulating fluidized bed boilers , the characteristics of high efficiency. In recent years, it has been vigorously promoted and used in my country.
The main problems of circulating fluidized bed boilers exposed in the field are frequent furnace wall accidents, resulting in poor operation reliability, short operation periods, troublesome repairs, and high costs.
In the circulating fluidized bed boiler, the bed material in the furnace rises along the furnace under the high temperature flue gas, and enters the two cyclone separators on the rear side respectively through the upper flue gas outlet of the rear water wall for gas, solid and phase separation. It is not separated. The solid particles are returned to the lower part of the furnace through the return valve. During the operation of the circulating fluidized bed boiler, the solid bed material containing fuel, combustion ash, limestone and reaction products flows in the furnace—cyclone separator—return material to moisten ——The closed circulation loop of the furnace is in constant high temperature circulating flow, and efficient combustion and desulfurization reactions are carried out. In addition to the circulating flow of the bed material in this loop, under the action of gravity, it flows along the four walls of the furnace. Continuous internal circulation, so the service life of the boiler lining refractory is the main factor for the normal operation of the boiler
Factors, wear resistance, pressure resistance and thermal shock properties of refractory materials directly affect the safety and service life of boiler operation.
Our company (Quantong Kiln Industry Co., Ltd.) has done in-depth research and continuous experiments on the refractory lining of circulating fluidized bed boilers in recent years, and now has a series of special wear-resistant circulating fluidized bed boilers with good practical effects. The manufacturing and construction technology of refractory and thermal insulation materials has achieved good results in many manufacturers.
The refractory materials used in different parts of the circulating fluidized bed boiler and different working atmospheres can be divided into the following parts:
Thermal shock series castables and plastics
Generally, circulating fluidized bed boilers are ignited under the bed, and the temperature rises rapidly during ignition, and then drops rapidly after ignition; therefore, the requirements for the thermal resistance of refractories in the air chamber, igniter, folded flame angle and other parts are relatively high, and large tonnage is required. The temperature in the boiler air chamber is very high when igniting, because of the high requirements for the fire resistance of the materials. The thermal shock-resistant casting qt-krs1 developed by our company can be used for circulating liquid bed boilers with a tonnage below 220t\/h, qt-krz2 And qt-krs2 is used for circulating fluidized bed boilers with tonnage above 220t\/h.